Beyond Extraordinary.
We believe in you, the rider. You are the best person to design your bespoke custom bike. Our mission is to empower you to direct the design of your bike – tuning it to your specific needs. The end product is uniquely precision crafted together with you, for you.
01
Introduction
Globally our retailers are equipped with our world leading design portal and configurator where we can visualise different ideas to create your dream Bastion. Upon receipt of deposit you will receive your Amulet, your bespoke symbol of ownership, granting you access to the Design Portal, where you can finalise the details of your Bastion together with our team of experts.
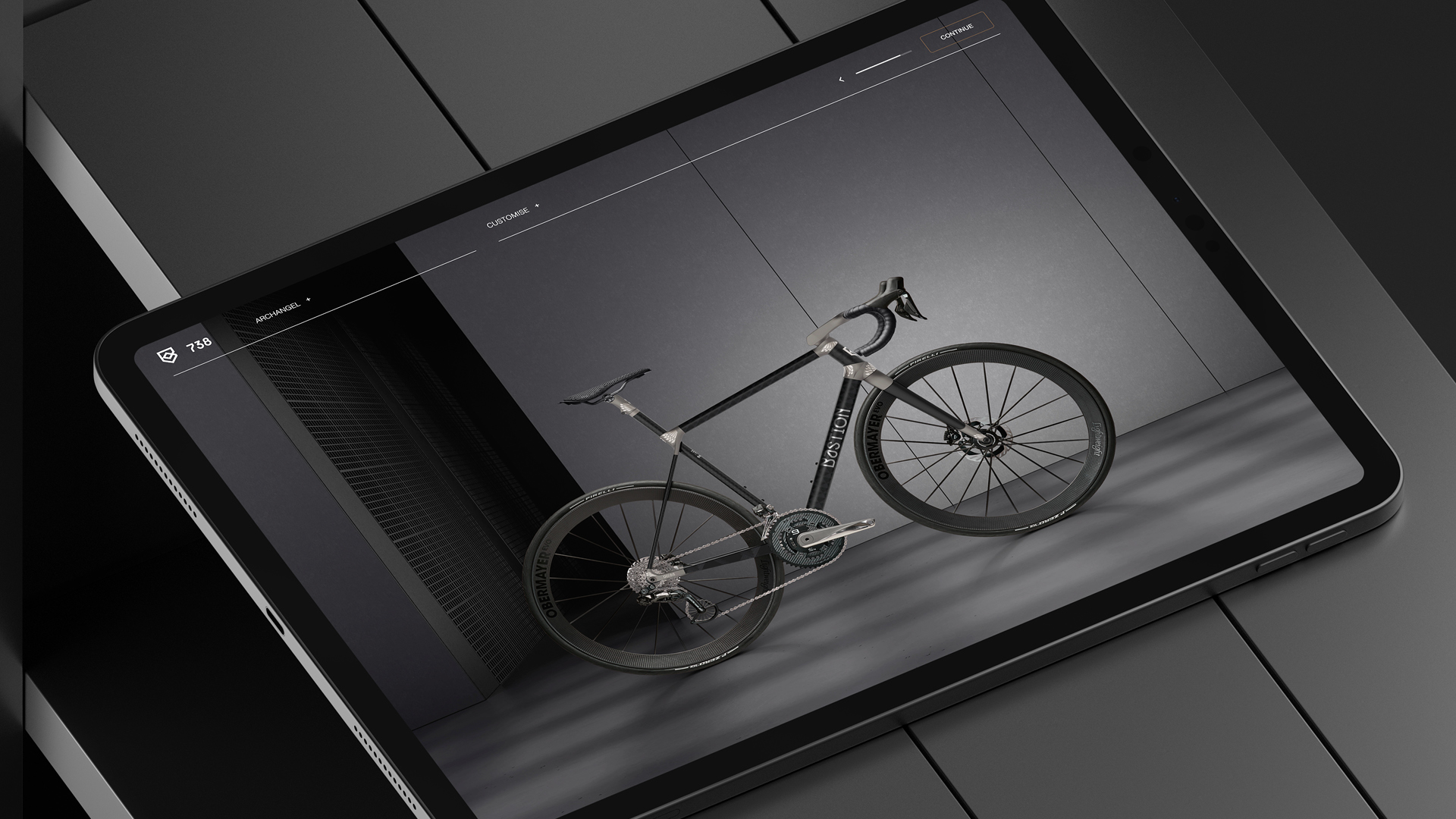
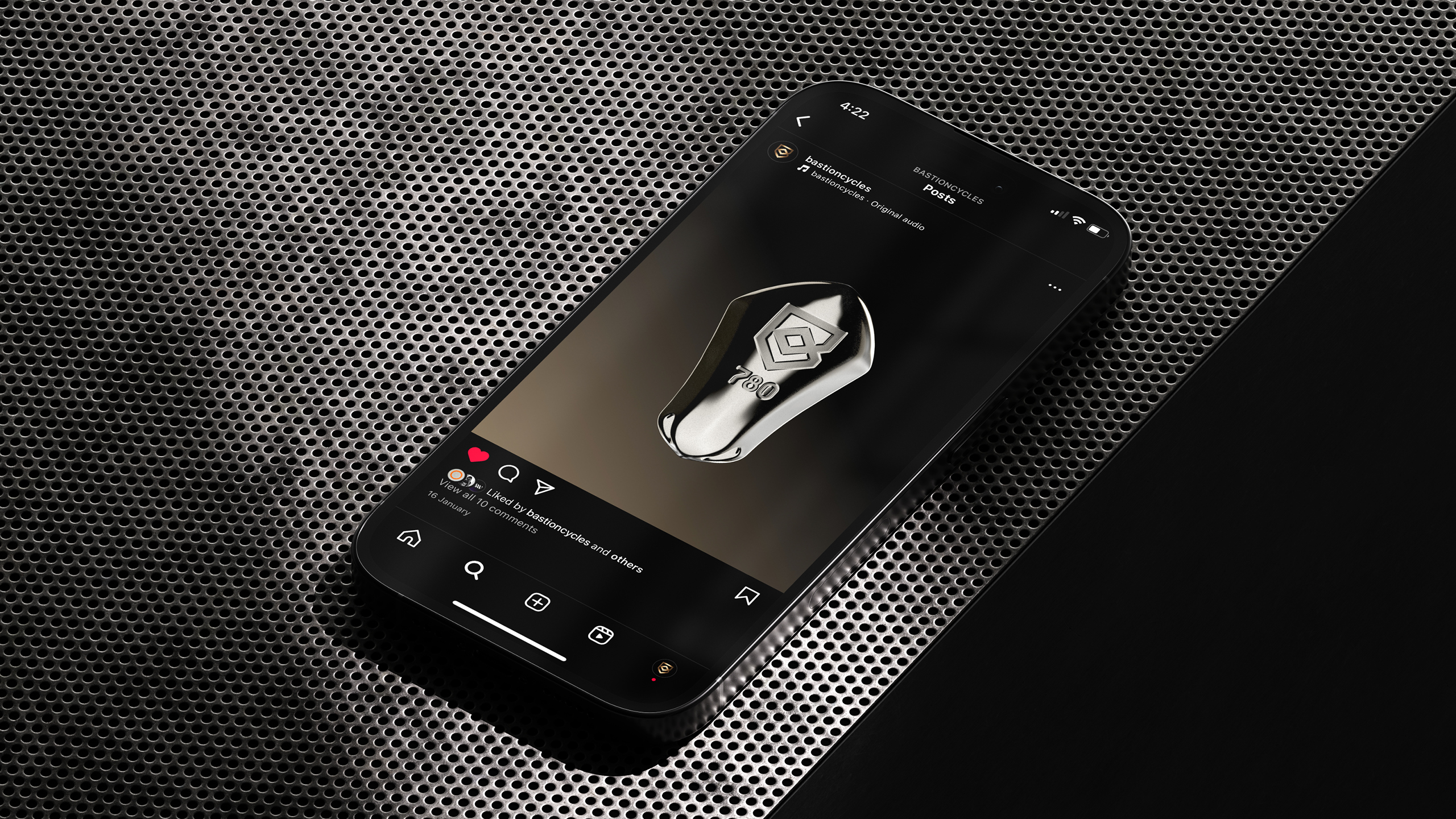
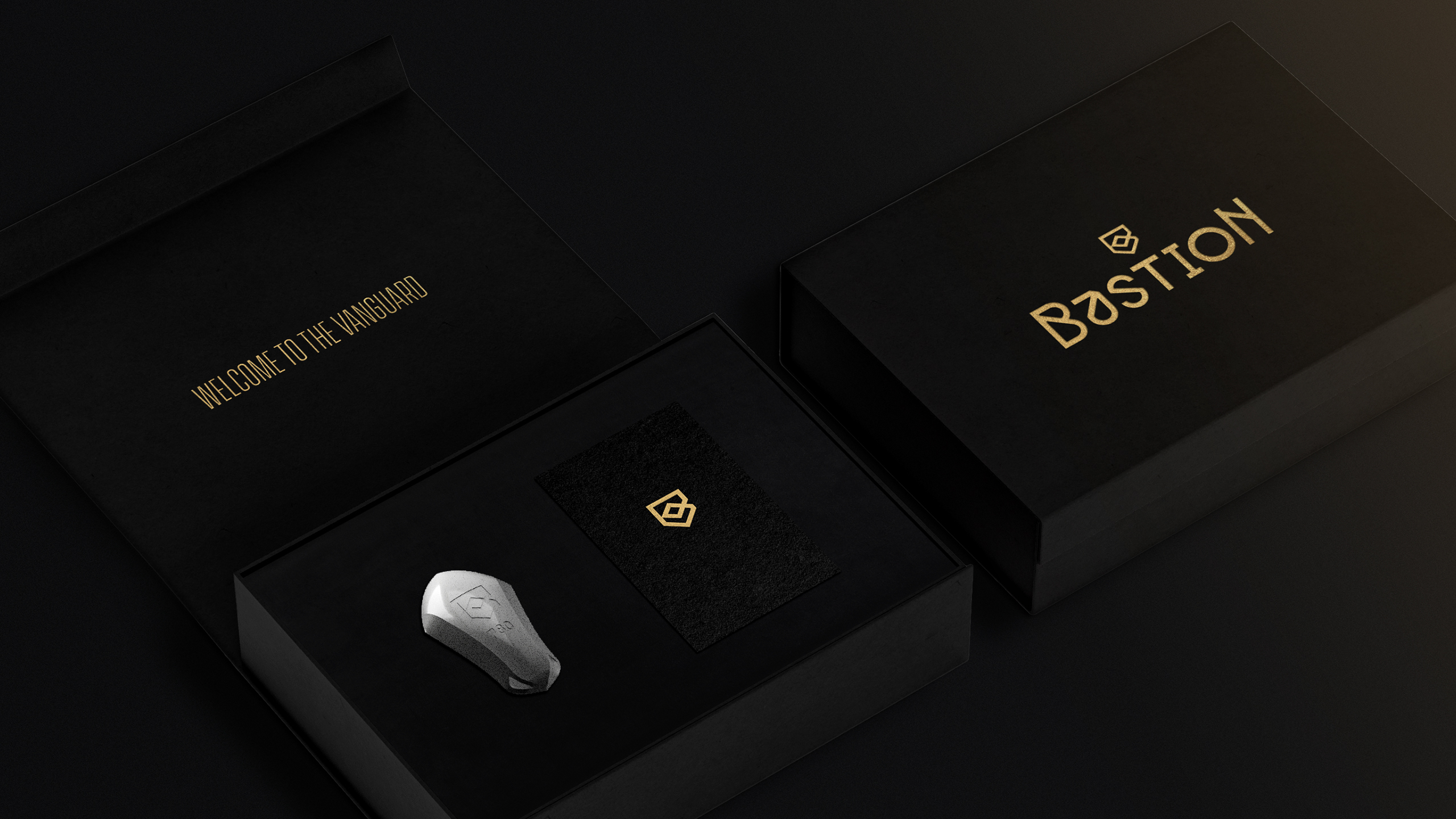
02
Design
Our meticulous design process ensures every Bastion is uniquely tailored to its rider. To enhance the order capture process we have created the world’s best design portal and configurator, empowering you to direct the design of your Bastion, tuning it to your needs.
Choose from over 1 million colour combinations in both raw and painted finishes in gloss and matte. Personalise your dropouts with your name, initials or an inspirational message. Every choice is rendered in photo-realistic imagery allowing you to visualise your dream bike in real time.
Select from the best components from the best brands. Opt for a top electronic groupsets from Shimano, SRAM, and Campagnolo and wheels from Partington, Princeton and Lightweight. Choose options from Ceramicspeed for Oversized Pulley Wheels and our own BC-01 SRM Powermeter cranksets.
Once we have received your order, we use state of the art computer modelling software to create a 3D model of your Bastion and simulate how it will look and perform on the road. We then provide a detailed Engineering Report covering geometry, stiffness and handling characteristics for you to approve before we begin production.
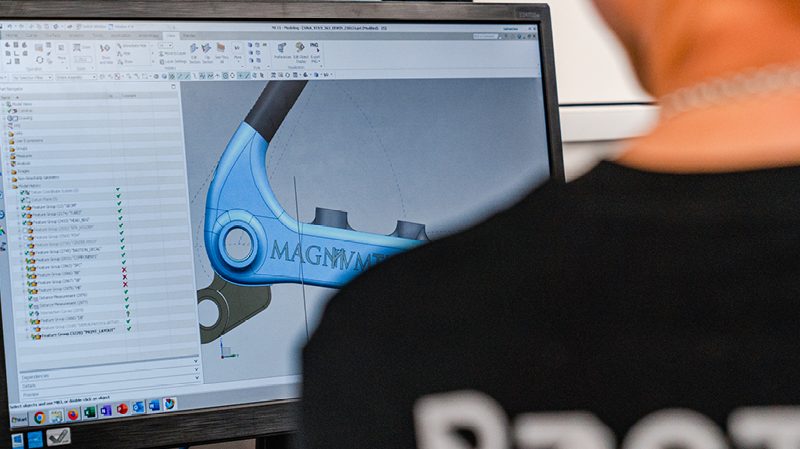
03
Manufacturing
Our advanced manufacturing process from 3D Printing and CNC machining to polishing and painting requires over 130 hours of precision work by precision machines. A further 70 hours of meticulous craftsmanship is required to sculpt and hand finish every Bastion.
Bastion lugs
Our lugs are a distinctive hallmark of our craftsmanship, showcasing our engineering and attention to detail. The lugs, which connect the tubes of the frame, are 3D printed in aerospace Grade 5 Ti6Al4V Titanium alloy, ensuring exceptional strength and durability while minimising weight.
The use of 3D printing allows for intricate designs that would be impossible to achieve with traditional manufacturing methods. The lugs are designed to enhance both the aesthetics and functionality of the frame, with smooth transitions that optimise both the power transfer and ride quality.
Internally the unique lattice structure not only provides structural integrity during manufacturing, it increases the stiffness of the lugs.
Following printing and machining, each lug is hand finished by skilled craftspeople contributing to the bespoke finish, ensuring every Bastion is as much a piece of art as it is a high performance machine.
Bastion tubes
Our tubes are crafted in carbon fibre, meticulously engineered to deliver the perfect balance of strength, stiffness and lightweight characteristics. Each tube is wound layer by layer in carbon fibre over a mandrel in a computer controlled process called filament winding. Enabling precise fibre orientation and continuous fibre paths and ultimate control of the performance characteristics of each bike.
The tubes are designed to smoothly transition to the titanium lugs, and by varying lay-ups and fibre modulus we are able to optimise the overall performance and comfort. The final matte or gloss finish on the tubes, either in a transparent clear or candy finish, or painted in a solid colour further reflects our commitment to produce frames that are as visually stunning as they are technically advanced.
Bastion frames
Once the lugs and tubes have been carefully prepared and quality inspected they are hand assembled in a bonding process developed in the automotive and aerospace industries. A carefully selected and stringently tested epoxy is used to bond the tubes to the lugs in a precise fixture where they are held for a minimum of 12 hours to ensure the geometry is millimetre perfect.
After bonding the frame, fork and barstem are post cured to maximise the strength and temperature resistance of the bonds. We then put every component through our stringent quality control checks which include rigorous measurements and proof load tests to guarantee the strength and quality before releasing for final finishing.
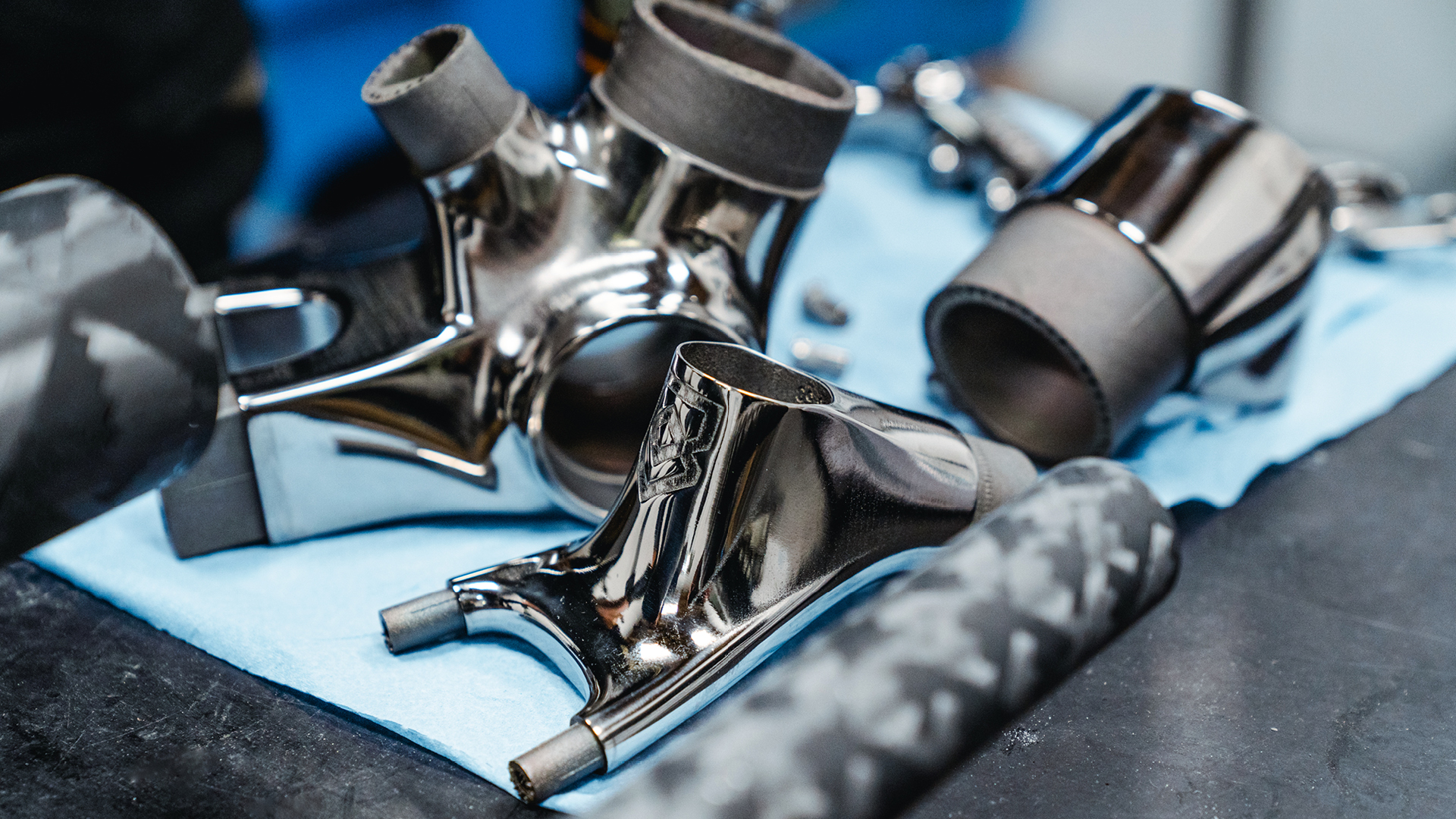
04
Finishing
Our paint process is a highly personalised craft, designed to enhance the unique identity of every Bastion. Once the frame is assembled, it is prepared for painting, with many hours spent meticulously masking, and sanding and smoothing the surfaces in preparation for paint.
Our skilled artisans then carefully apply multiple layers of automotive grade paint, carefully building up colour and depth to achieve a smooth and even finish. The colours are often customised to the owner’s specifications, allowing for a wide range of possibilities – from classic, understated hues to bold, striking metallics and pearls. In some cases bespoke graphics are added further personalising the design.
Throughout the process every detail is scrutinised and assessed, chasing perfection. The end result is a finish that is not only visually stunning, but also resilient against the elements reflecting our intent to create works of art you can ride in any weather.
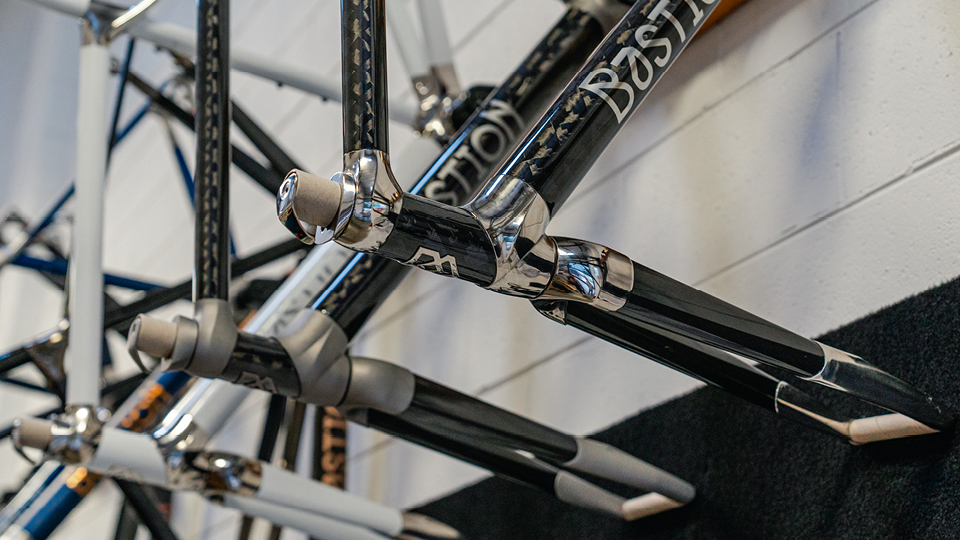
Bastion Foundry
Our new manufacturing facilities are being built as a state-of-the-art blend of advanced technology and artisanal craftsmanship, located in Melbourne, Australia. The Bastion Foundry is equipped with cutting-edge technology, including Titanium 3D Printers, CNC Machines, Filament Winders and a Downdraft Paint Facility which allow for precise manufacturing of custom components.
The space is designed to optimise the flow of production from initial design to final assembly and quality control. Each area is meticulously organised, with dedicated areas for each stage of the process, including individual clean rooms for 3D Printing, Composites, and Bonding. Every aspect of the Foundry reflects our commitment to precision, innovation and the highest quality standards, ensuring every Bastion produced is a true work of art.
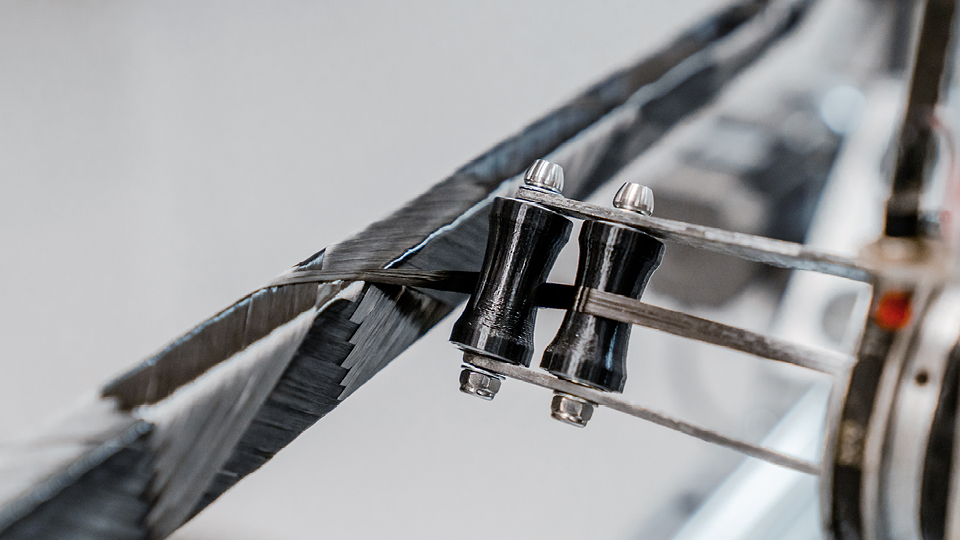
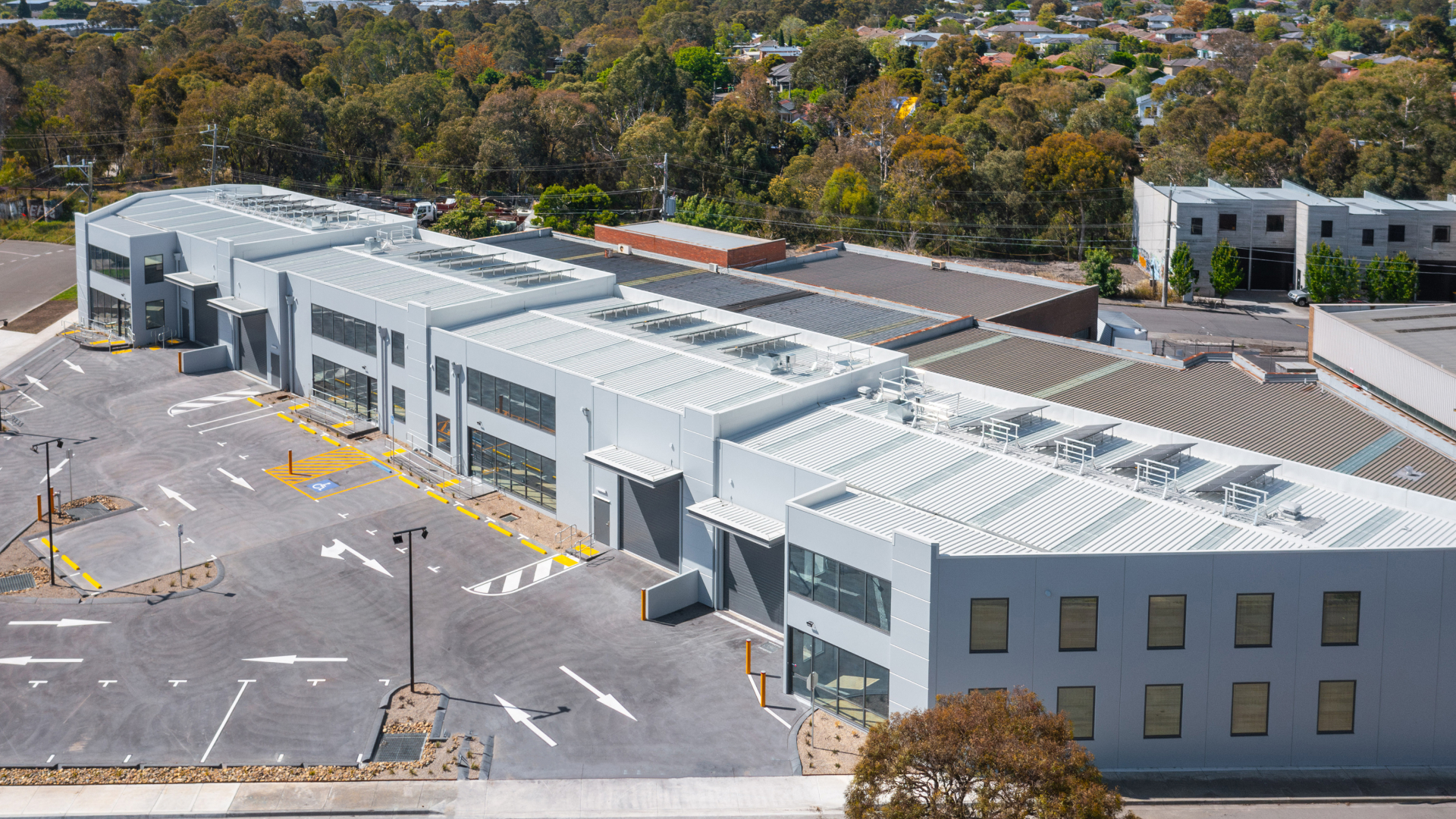
Forge your
own path
For any enquiries or questions, please reach out to the Bastion team. Follow along with our journey via social media.